Water Damage Restoration Los Angeles requires an extensive list of tasks that can include drywall and ceiling repair, carpet or flooring replacement, repainting, and other similar projects. The water and materials can harbor bacteria and other toxins that promote mold growth, so they must be sanitized thoroughly.
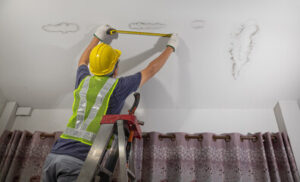
Before professionals arrive, homeowners can do a few things to help mitigate the damage. Start by shutting off the water source, and ventilating the area to reduce mildew and mold.
Before a professional water restoration contractor starts any work, they should perform a complete inspection of the affected areas. This will help them determine the source of the water and categorize it according to its level of contamination. It will also allow them to assess the structural integrity of the building and identify any potential safety hazards or health concerns.
After identifying the source of the water and its level of contamination, they will begin the process of water extraction. This will involve using specialized equipment to remove the excess water and to drain water-logged areas of the property. They will also use moisture meters to check for hidden pockets of saturation that may need extra attention.
Once the excess water has been removed, they will focus on drying the space and preventing mold growth. They will use industrial-grade air movers and dehumidifiers to speed up the drying process, as well as monitor moisture levels in hard-to-reach areas. They will also use sanitizing and deodorizing techniques to sanitize the area and remove any lingering bacteria or contaminants.
This step is important because the longer a space remains saturated with water, the greater the chance of secondary damage and mold growth. It is also crucial to identify any electrical hazards and ensure that all damaged materials are removed and disposed of safely.
It is a good idea to take photos of the areas affected by the water damage before starting any repairs or cleaning. This will help you prove the extent of the damage to your insurance company, if necessary. Additionally, it is a good idea to remove any valuable or personal items from the affected areas before beginning any inspections. This will prevent them from being accidentally ruined by water or dirt.
Extraction
Water extraction is a vital step that helps to prevent further damage and reduce the risk of mold growth. It involves using submersible pumps and industrial vacuums to remove excess water from the affected areas of a home or business. This step also ensures that contaminated materials, such as insulation and drywall, are removed and replaced.
Before beginning the water extraction process, it is important to make sure that all safety hazards are addressed. This includes shutting off electricity, especially if it has been exposed to standing water for more than 48 hours. In addition, it is important to check the contents of the home or office to determine if any items can be saved. This can include papers, photographs and other personal items that may be salvaged as long as they are cleaned and treated immediately.
Once the removal of excess water is completed, the restoration crew will begin to dry out the property. This is a time-consuming process that involves specialized equipment, such as air movers and dehumidifiers. It is important to ensure that all moisture is eliminated, as it can lead to critical structural damage and accelerate mold formation.
Once the property has been completely dried, it is important to sanitize the area to eliminate bacteria buildup and odors. This step can be done using Environmental Protection Agency-approved disinfection and sanitization solutions. These can be administered through foggers, which transform chemicals into a mist that effectively kills odor-causing bacteria. This is a very crucial step in the water damage restoration process, as it can help to reduce health risks associated with toxic mold and bacteria. It is also important to note that many homeowners’ and business owners’ insurance policies will cover the cost of professional water damage restoration services.
Drying
Once the bulk of the water is removed, it’s time to start drying the affected areas. This is done to prevent irreversible damage such as swelling of porous materials, shrinkage of some fabric materials, and rusting of metal accents. If left unchecked, these problems can cause serious structural damage and mold growth, both of which are expensive and difficult to correct.
The process begins with a thorough inspection of the property. This includes identifying and stopping the source of water, as well as checking for any secondary damages such as stains from sewage or mud. Once the source is stopped, a variety of equipment may be used to remove remaining water. This can include submersible pumps if the water level is high, wet/dry vacs if it’s low, or a mixture of both.
After all the water is removed, the space must be ventilated. This can be done by opening windows and doors as long as the weather permits. In some cases, removing baseboards and molding may also be necessary to permit adequate ventilation. The area must also be sanitized, and this might include steam cleaning or commercial sanitizing solutions.
Once the space is dry, professionals can return to perform more detailed inspections and make decisions about what needs to be repaired or replaced. For example, if walls are severely damaged by water, they may need to be replaced entirely. Likewise, items such as furniture, carpeting, and draperies might need to be removed and stored away until they can be cleaned, dried, and restored. A professional water restoration company can help you recover from your water loss by restoring your property to its original condition.
Cleaning
After the water has been removed, it is necessary to clean and sanitize the affected areas. This will help to prevent mold and mildew from growing and may include using disinfectants, dehumidifiers, and fans. It is also recommended that homeowners open windows and doors to allow for air circulation.
The cleaning process can be very involved and requires specialized equipment and techniques. It is best left to professionals who have the equipment and experience to handle the task safely and effectively. The first step is to determine the source of the water damage and identify any potential safety hazards. This can be done by looking for signs of mold, such as discoloration or a musty smell.
It is also important to check for the type of water that has contaminated the area. There are three different types: clean, gray, and black. Clean water is from a source such as rain or leaky pipes. Gray water is contaminated from appliances such as toilets or washing machines. Black water is toxic and is from sewage or flooding. It is unsafe to touch and can contain harmful bacteria, viruses, and toxins.
Once the area has been cleaned and sanitized, it is necessary to dry out the affected areas. This can be done by opening windows and doors, using dehumidifiers and fans, and mopping up the excess moisture. It is also recommended that homeowners use paints that are designed to withstand moisture and drywall made from materials that can resist water damage.
If the water damage is severe, it is important to contact a professional service provider as soon as possible. This will help to prevent further damage to the home or building, and it can also save money on future repairs.
Repairs
Once the water has been extracted and the area has been dried out, it is time to start repairing any damage. Flooring and walls may need to be replaced, possessions thrown away or stored elsewhere for safety, and structural elements like drywall or wood framing may need to be fixed.
This step is very important to prevent the growth of bacteria, mold and fungus that can cause illness in people and pets. Wet materials are breeding grounds for these organisms, and they can also lead to the deterioration of wooden structures and metal fixtures over time. If not taken care of immediately, they can become more serious problems that require expensive repairs and replacements in the future.
At this point in the process, a professional water damage restoration company should be able to provide you with a detailed estimate for any work needed and give you an estimated timeline for when the work will be completed. Depending on the amount of water damage, it may be necessary to temporarily relocate people and animals from the affected area while the work is being done. In many cases, homeowners can continue to live in their homes during the water damage repair and restoration process as long as they have access to another room or bathroom.
Water Damage Restoration is a complex task that requires training, equipment and experience to perform properly. If you’ve experienced a flood, water leak or other water catastrophe, call the water damage restoration experts at COIT to help restore your home, business or industrial facility back to its original condition. With over 70 years in the cleaning and restoration industry, our professionals are trained to remove excess water, dry and dehumidify the space, clean and disinfect surfaces, and perform any other necessary repairs for safe, fast and effective water damage restoration.